Labor Productivity Calculator
Productivity Results
Explore More:
- Productivity Calculator
- Productivity Percentage Calculator
- Healthcare Productivity Calculator
- Rehab Productivity Calculator
- Productivity Index Calculator
- Welding Productivity Calculator
Understanding Labor Productivity: A Comprehensive Guide
Labor productivity is a crucial metric that measures the efficiency of your workforce by evaluating the output produced relative to the labor input. Accurate assessment of labor productivity enables businesses to optimize operations, allocate resources effectively, and enhance overall performance.
What Is Labor Productivity?
Labor productivity quantifies the amount of goods or services produced per unit of labor input, typically measured in hours. The fundamental formula is:
Labor Productivity = Total Output / Total Labor Hours
For instance, if your team produces 10,000 units in 2,000 hours, the labor productivity is 5 units per hour.
How Is Labor Productivity Calculated?
Labor productivity is calculated by comparing the total output (goods or services produced) with the total labor hours used to produce that output. Here’s the step-by-step process:
✅ Determine Total Output: Measure the number of units produced or services delivered during a specific period.
✅ Measure Total Labor Input: Calculate the total hours worked by all employees involved in production.
✅ Apply the Formula: Labor Productivity=Total Output / Total Labor Hours
Example:
If your bakery produced 20,000 loaves of bread in a month and the team worked a total of 4,000 hours, the labor productivity would be: 20,000 / 4,000= 5 loaves per hour
This calculation helps businesses identify their workforce’s efficiency and track progress over time.
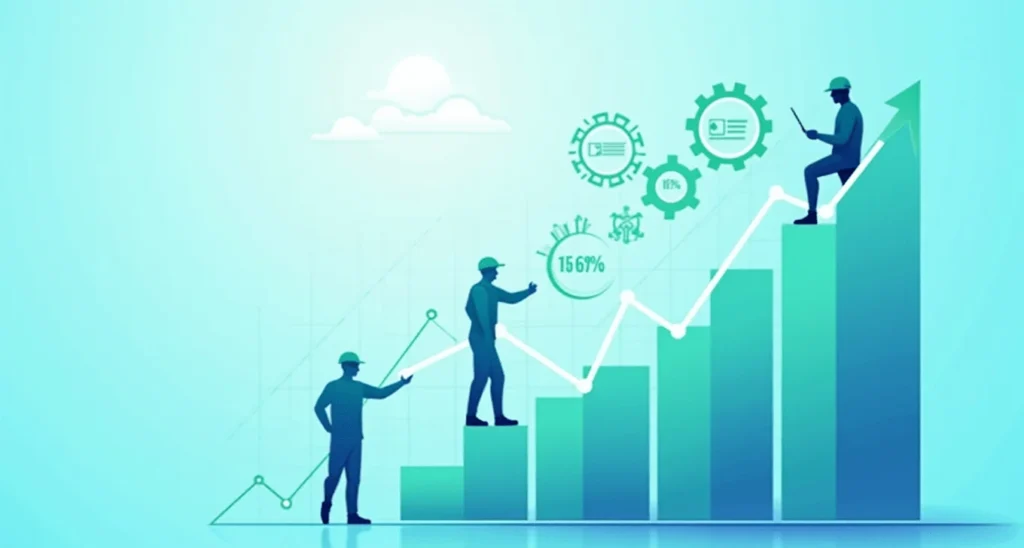
Types of Productivity Measurement
Understanding different productivity metrics provides a comprehensive view of efficiency:
- Partial Factor Productivity (PFP): Assesses output relative to a single input, such as labor or capital.
- Multifactor Productivity (MFP): Evaluates output against a combination of inputs like labor, capital, and materials.
- Total Factor Productivity (TFP): Considers all inputs to measure overall efficiency.
These metrics help identify specific areas for improvement and inform strategic decisions.
Factors Influencing Labor Productivity
Several elements impact labor productivity:
- Technical Efficiency: Effective utilization of inputs and processes.
- Education and Training: Skilled employees contribute to higher productivity.
- Capital Equipment: Advanced tools and technology enhance output.
- Work Environment: Optimal conditions, including adequate lighting and temperature, improve focus and efficiency.
- Motivation and Engagement: Employee morale directly affects performance levels.
Industry Benchmarks
Productivity standards vary across industries. For example:
- Manufacturing: Output per machine hour or per labor hour.
- Software Development: Lines of code written or features developed per developer.
- Content Creation: Articles or media pieces produced per content creator.
Understanding these benchmarks helps in setting realistic goals and evaluating performance.
Common Productivity Myths
It’s essential to debunk misconceptions:
- Myth: Longer working hours equate to higher productivity.
Reality: Efficiency and quality of work are more important than sheer hours logged. - Myth: Multitasking enhances productivity.
Reality: Focusing on one task at a time leads to better outcomes. - Myth: Skipping breaks increases output.
Reality: Regular breaks prevent burnout and maintain consistent performance.
Enhancing Labor Productivity
Strategies to improve productivity include:
- Implementing Training Programs: Regular skill development sessions.
- Leveraging Technology: Utilizing tools for automation and efficient workflow management.
- Setting Clear Goals: Establishing specific, measurable objectives for employees.
- Monitoring Performance: Regular assessments to identify areas for improvement.
- Fostering a Positive Work Environment: Encouraging open communication and recognizing achievements.